Cantor
Software for Windows, Doors and Shutters
Growing Your Fenestration Business
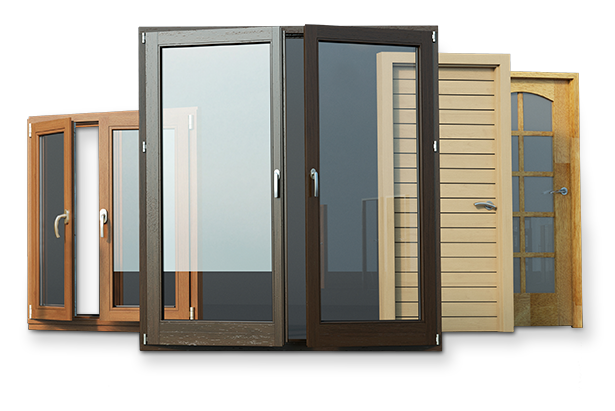
Find your system
A+W CANTOR ERP+CIM
In A+W Cantor ERP+CIM, your business processes are comprehensively mapped, leading to more effective production. The entire order processing, from quotation creation through order entry and credit limit checks to purchasing and materials management as well as invoicing, can be carried out almost paperlessly thanks to the integrated document archive. Just-in-time planning helps you always work on schedule and as needed, ensuring you keep an overview.
Modules
- Offer and order processing
- Purchasing and material management
- Processes and management
- Capacity planning and delivery date determination
- Work preparation and production control
A+W CANTOR DEALER CLOUD
A+W Cantor Dealer Cloud allows window manufacturers to provide modules to their dealers, enabling them to create quotes, orders, delivery notes, and invoices. Additionally, dealers can set up their own installation services and other basic items, as well as manage their customer base.
Modules
- Offer and order processing
- Service and installation planning
Add-ons
Cantor
iQuote
Your customers are accustomed to ordering products online 24/7. Leverage that buying habit utilizing A+W iQuote’s e-commerce store. This powerful e-commerce portal empowers window manufacturers to offer their dealers the convenience of generating quotations and placing orders for their customers, anytime, anywhere. Whether on-site at construction project or in the office, your dealers can access product configurations directly from your website, enhancing both customer service and optimized efficiency.
A+W iQuote seamlessly integrates with the A+W Cantor system, ensuring that data displayed in the e-commerce store is sourced directly from the A+W Cantor database. Orders placed through A+W iQuote are instantly visible in the A+W Cantor system, eliminating the need for duplicate order entry and enabling real-time scheduling for production.
- Seamless integration with A+W Cantor eliminates duplicate master data creation and maintenance for the e-commerce store
- Expansion of sales channels and customer reach
- Intuitive user interface requires no training
- Conduct price calculations and construction feasibility tests, mirroring A+W Cantor order entry
- Streamlined order processing, leading to faster and easier operations
- Direct transfer of e-commerce store orders for production planning
- Drastically reduced time-to-market for new products through web-based configuration
Cantor
A+W Cantor integrates administration and production: from creating quotations, entering orders, and production, on through to delivery and assembly, the whole process is mapped.
With what we have created with A+W Cantor, we are the market leader when it comes to configurators.
Part of the benefit of A+W Software is that when you (expand) to a new location, all of the master data set up for our business process are pre-built (…) The A+W software will guide any new potential operation forward rather than having to start from scratch. Software, at the end of the day, is the core to everything we are! It has been an enabler for all of our visions and dreams as well as what we want. It helped us accomplish it a lot faster than we anticipated.
Cantor
Cantor Smart Companion
A+W Cantor Smart Companion for A+W Cantor is currently available for both Production and Stock.
In the production area, utilize the app within the dispatch warehouse to efficiently book finished elements and accessories onto racks and allocate them to specific dispatch areas. Benefit from the continuous mode feature, thus allowing simultaneous scanning of multiple elements using the smartphone camera. Functioning as a mobile info terminal (read mode), the app provides valuable support by displaying production status updates for individual order items or objects located on racks. This ensures real-time tracking of element whereabouts during production. Material requisition is streamlined by scanning barcodes at predefined registration points.
Dynamic forms feature prominently in A+W Smart Companion, enabling user input via selection lists, checkboxes, sliding buttons, etc. Users have the flexibility to customize forms to suit specific requirements. Additionally, streamline complaint management by capturing complaints with accompanying photos directly within the app, thus seamlessly transmitting them to A+W Cantor CIM without redundant data entry.
Covering tasks in the stock area, including goods receipt, material transfer postings, and inventory postings, the mobile app, facilitates comprehensive refining of these processes. Easily access an overview of all counted items with data seamlessly integrated from A+W Cantor for immediate availability.
- Minimal learning curve thanks to the use of a familiar, everyday device
- Increased employee productivity facilitated by a user-friendly app
- Time-saving benefits achieved through rapid scanning of multiple barcodes (continuous mode)
- Gain an information advantage with quick and convenient access to element status and location at any time
Cantor
A+W Cantor integrates administration and production: from creating quotations, entering orders, and production, on through to delivery and assembly, the whole process is mapped.
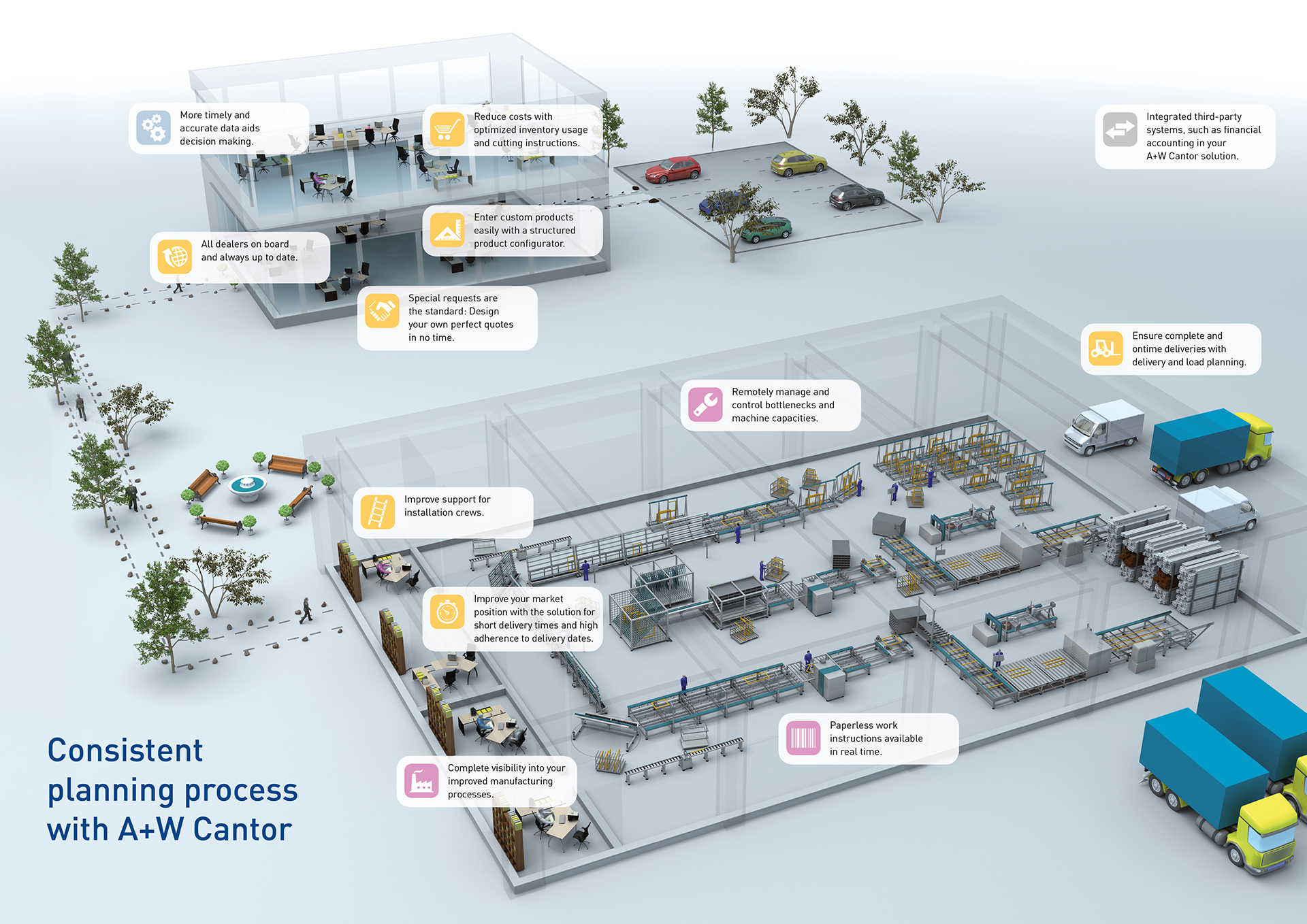
Satisfied Customer Voices
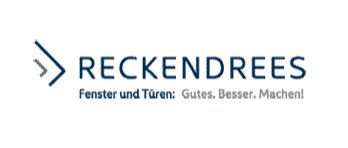
A+W Cantor Reference
Reckendrees Bauelemente
The clever CIM system is an important plus point for A+W Cantor. Where other production systems only show an itinerary sheet on the workplace screen, the employee at the A+W Cantor monitor sees the entire parts list if required – the system has a very flexible design. It has also been impressive with the brilliant adjustable plausibility tests, which is particularly important for us in special construction.
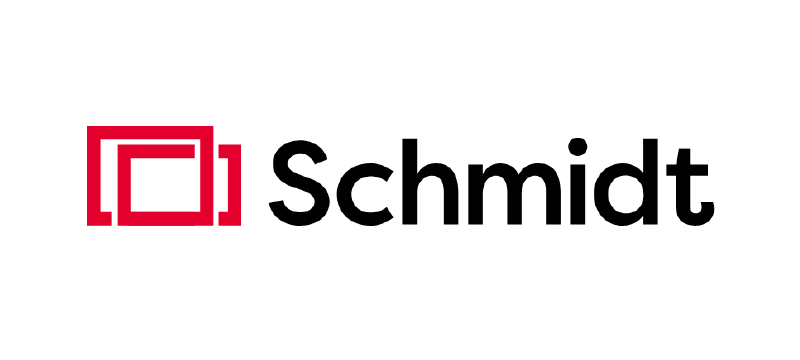
A+W Cantor Reference
SCHMIDT
The outstanding materials management allows us to remove and manage material via BOMs. This helps us with reliable materials planning.
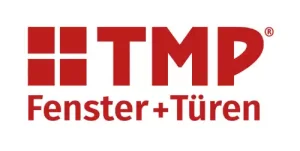
A+W Cantor Reference
TMP Fenster + Türen
Since the introduction of the A+W Cantor System, our production staff has taken it for granted that all parts are available exactly where they are needed.
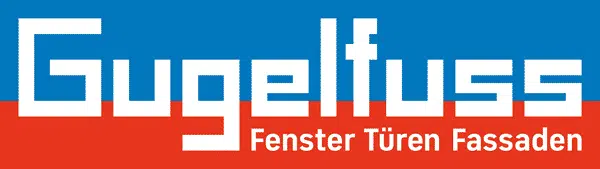
A+W Cantor Reference
Gugelfuss
There is no building block that we cannot handle with the A+W Cantor Software. We work almost 100% with A+W Cantor.